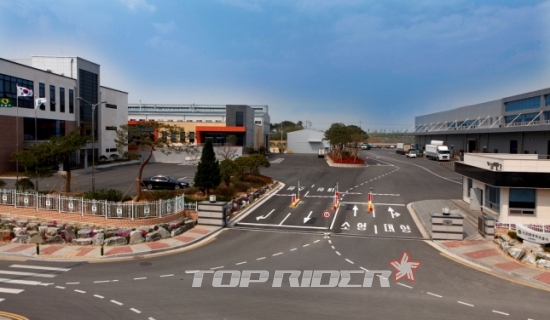
자동차를 타거나 운전하다 보면 알겠지만 완벽히 매끈하게 포장된 도로는 거의 없다. 과속방지턱부터 불규칙하게 튀어나온 요철 그리고 심지어 비포장도로 같은 악조건까지 자동차는 아무 이상 없이 주행을 해야 한다.
자동차에 대한 지식 중 우리가 흔히 알고 있는 서스펜션은 자동차의 무게를 지탱하고 충격을 흡수하는 스프링, 그리고 스프링의 움직임을 제어하는 역할을 하는 쇽업쇼버로 구성되어 있다. 둘 중에 하나라도 빠지면 어떻게 될까? 사실 쇽업쇼버가 없어도 운행은 가능하다. 그러나 스프링 없이 운행은 불가능하다. 이유는 스프링이 없으면 자동차를 지탱할 수 없어 차체가 지면에 그대로 닿기 때문이다.
1946년에 처음 설립된 대원강업은 우리나라에서 특수강을 생산하는 곳이 없어서 열차 레일과 바퀴를 압연해 스프링으로 사용했다. 이후 6.25 전쟁이 일어날 때 공장이 파괴되는 불운을 겪기도 했지만 파괴된 공장을 복구하고 시발자동차에 스프링을 납품하면서 스프링 전문 기업으로 발돋움하게 되었으며 이후 1964년 처음으로 해외 수출길을 열었다. 그리고 1967년에 설립한 현대자동차에서 생산하는 차종의 스프링을 개발 및 납품하게 되었고 현대자동차 설립 후 지금까지 대원강업과 현대자동차는 서로 긴밀하게 협력하고 있다.
대원강업은 뛰어난 기술력을 인정받아 1993년 상공의 날 금탑산업훈장을 수상했으며 2008년 협력사 대상을 수상, 그리고 2013년 현대자동차와 공동 개발한 '자동차 엔진용 고강도 경량 밸브스프링'을 통해 IR25 장영실상을 수상하기도 했다.
대원강업은 이번에 기자단이 견학한 천안공장을 포함하여 인근에 있는 성환 그리고 창원에 공장이 있으며 해외에서는 중국, 미국, 인도, 폴란드, 러시아에 현지생산 공장이 있다.
대원강업이 생산하는 품목은?
대원강업의 매출 절반을 차지하는 스프링은 바로 자동차 등에 쓰이는 현가 스프링이다. 현가 스프링은 우리가 흔히 승용차에서 볼 수 있는 코일 스프링, 무거운 화물을 적재하는 상용차에 쓰이는 판 스프링, 에어백에 공기를 주입하는 에어 스프링 등이 있다. 위 사진이 자동차에 가장 많이 쓰이는 코일 스프링이다.
그리고 위 사진이 바로 여러 장의 판을 쌓거나 묶은 판 스프링이며 주로 무거운 화물을 적재하는 트럭이나 많은 승객이 탑승하는 버스에 이용된다. 최근에는 보다 높은 응력을 갖춘 소재를 쓴 파라보릭 스프링 그리고 판 스프링끼리 결합한 서스펜션 키트를 개발하여 적용하고 있다.
서스펜션 뿐만 아니라 엔진 내부의 밸브를 제어하는 밸브스프링을 생산 납품하고 있다. 자동차 엔진의 연소효율성을 높이기 위해 엔진의 밸브스프링은 점점 경량화되고 있으며 작년에는 현대자동차와 공동 개발을 통해 더 강하고 더 가벼운 고강도 밸브스프링을 개발하기도 했다.
밸브 뿐만 아니라 자동차에 탑승할 때 탑승자의 편안함을 보장하는 자동차 시트도 개발 공급하고 있다. 시트는 대원강업 전체 매출액의 15%를 차지하고 있다.
자동차는 물론 열차 승객들을 위한 시트도 제작 납품하고 있으며 전철부터 KTX까지 다양한 열차 시트를 제작하여 공급하고 있으며 시트는 이번에 견학한 천안공장이 아닌 인근의 성환공장에서 모두 생산하고 있다.
스프링, 스테빌라이저 바 생산 공정을 둘러보니
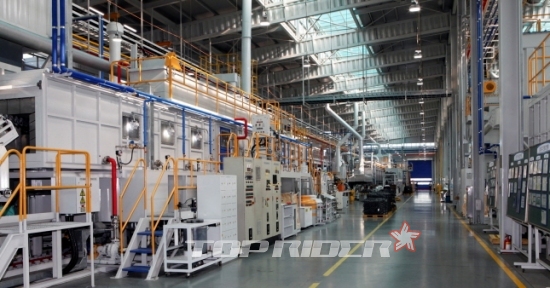
이번에 견학한 대원강업 천안공장은 주로 자동차의 서스펜션 스프링, 스테빌라이저 바를 생산하는 설비를 둘러보게 되었다. 규모가 큰 협력업체의 경우 완성차 메이커처럼 사람 대신 로봇이 주로 생산과 조립을 담당하는데 대원강업 또한 대부분 공정이 자동화로 이루어졌다.
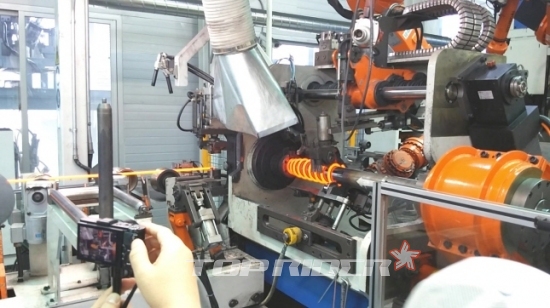
자동차 서스펜션에 쓰이는 스프링은 일자 모양의 특수강을 가공하기 쉽도록 매우 뜨겁게 달군 후 원통에 감아 형상을 미리 만든 후 다시 열처리 가공을 한 뒤 도료를 입히면 완성된다. 얼핏 별거 아닐 수도 있겠지만 코일 스프링은 1톤이 넘는 무거운 자동차 무게를 오랜 시간이 지나도 변형 없이 지탱해야 하기 때문에 일반적으로 자동차 차체에 쓰이는 강판보다 훨씬 더 장력이 강한 초 고장력 특수강을 사용하며 스프링의 경우 2,000MPa, 스테빌라이저 바는 1,500MPa 이상의 초 고장력 특수강을 사용한다.
매우 혹독한 제조 과정을 거친 코일 스프링은 현대자동차가 조립하는 쏘나타에 장착된다. 스프링이 완성되었다고 끝이 아니다. 스프링을 반복적으로 누르면서 제품테스트를 거친 뒤 현대자동차에 공급된다.
스프링과 함께 어떤 주행상황에서도 자동차의 평형을 유지시켜주는 스테빌라이저 바를 생산하는 장면이다. 요즘 고속주행, 또는 와인딩주행에서 주행안전성을 높이기 위해 스테빌라이저 바의 강성 또한 점점 높아지고 있는 추세이다. 다만 스테빌라이저 바의 경우 너무 강성이 높으면 승차감이 떨어지고 스프링이 부드러운데 스테빌라이저 바 강성이 지나치게 높은 경우 자칫 전복될 위험도 있기 때문에 스프링보다는 장력을 조금 낮게 설계를 한다. 모양과 쓰임새는 스프링과 다르지만 스테빌라이저 바도 스프링과 생산 과정은 비슷하다고 한다.
혹독한 테스트과정을 실시하는 대원강업 R&D 센터
생산공장 옆에 나란히 들어선 R&D 센터는 다양한 제품 테스트를 실시한다. 여기서는 금속시험과 신뢰성평가를 진행하며 금속시험은 주로 스프링강의 품질 평가를 목적으로 금속현미경 등을 통해 미세조직 관찰, 성분분석, 압축 잔류응력 측정 등으로 이루어진다.
신뢰성 평가는 일반 내구시험을 통해 스프링의 내구성 및 상관 부품과의 연관성, 스테빌라이저 바 바의 경우 차량의 장착상태와 동일한 조건 하에서의 내구성과 이음평가를 실시한다. 스프링과 스테빌라이저 바 둘 다 압축테스트를 30만회 이상 실시하게 된다.
자동차는 환경 및 주행 조건에 따라 금속의 내구성에 해가 되는 바닷물 그리고 염화칼슘 등에 노출되며 장마철의 높은 습도, 고온 등의 조건에도 노출된다. R&D 센터에서는 이러한 특성을 고려하여 소금물은 물론 고온과 높은 습도에 노출되는 병행테스트도 실시하고 있다고 한다.
앞으로 대원강업의 과제는 경량화
위 사진의 스프링을 자세히 보면 오른쪽 노란색 스프링은 다른 스프링과 달리 스프링 내부에 홀이 있다. 차이점이 있다면 무게가 기존 스프링보다 더 가볍다는 것인데 기존 스프링과 강성 및 탄성 계수가 동일하면서도 무게를 줄여 경량화를 실현했다는 점이다.
현재 자동차의 연비를 높이기 위한 수단으로 완성차 메이커들은 자동차의 무게를 조금이라도 더 줄이려는 노력을 하고 있다. 대원강업은 완성차 메이커들 행보에 맞춰 자사가 생산하는 제품의 경량화를 이루면서도 신소재 사용을 통해 품질과 내구성을 끊임없이 높이고 있다.
대원강업 성열각 사장은 “지난 오랜 시간을 현대자동차그룹과 함께 하면서 발전한 기술력으로 이제는 세계 정상 수준의 부품업체라고 자부한다”며 “세계 여느 스프링메이커와 견주어도 손색이 없을 정도로 우리만의 분명한 경쟁력을 갖추고 있다”고 말했다. 특히 천안지역으로의 공장이전은 본사와 생산공장, 그리고 R&D를 한 울타리 내에 둠으로써 또 다른 경쟁력과 시너지를 창출하고 있다”고 강조했다.
김진우 기자 〈탑라이더 kimjw830@top-rider.com〉